Chonkiii
Robot Facts
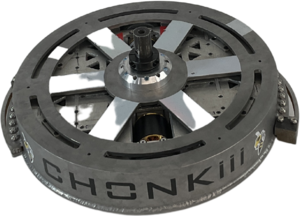
[[File:Chonkiii-TaperedShell.png|thumb|Chonkiii With Tapered Shell] Chonk
Builder | RoboJackets (See below for members) |
Drivers | Brian Epstein, Jacques Wang |
Weight Class | 30lb |
Body Material | Aluminum Chassis, 4140 Shell |
Weapon | Shell Spinner |
Weapon Drive | 2 X Scorpion 4035-380KV, Friction Drive |
Drive | Turnigy Aerodrive 4250-500KV, Dual Cam Shuffler |
Power | Weapon: 6S 2000mah MaxAmps for each weapon, Drive: 5S 3250mah MaxAmps |
Transmitter/Receiver | Taranis Q X7, FrSky X8R |
Members:
- Sydney Bakey (Lead)
- Mihir Nagaraj (Mentor)
- Brian Epstein (Mentor)
- Janie Edgar
- Jacques Wang
- Cade Tyler
- Dan Vail
- Christopher Bellflowers
- German Ortega
- Andrew
- Gray
- Maddie
Overview
Concept Motivation
Chonki as a concept started as a name and not a design. Brian initially thought "Hey, it would be really funny if we named a robot Chonki and made it really, really big and really really loud..." The more practical goal of Chonki was to utilize the 1.5 times weight bonus from not using wheels for movement to evaluate shell spinners. In its second iteration, Chonkii lived up to its name and goal, attracting many viewers and hearing protection at competition due to the loud noise of the shufflers on steel floors. While Chonkii did manage to achieve many of its goals and function during competition, it had much room for improvement. In its third iteration, Chonkiii’s concept motivation is simplistically to take Chonkii, make it work, and make it work even better.
Purpose
Chonkiii is the third iteration of a 45 lb shuffling shell spinner BattleBot. The robot consists of a chassis that remains stationary relative to the ground and a rotating steel shell that surrounds the entire robot. Chonkiii aims to improve on the design of the previous iteration’s shuffling module by improving the components or areas we ran into issues with in competition. The goal is to design and implement a self-righting mechanism, a more durable shell, faster drive, and superior traction on the feet.
Now that Chonkii has seen competition, much of our design process focused on improving its durability and compatibility in competition. The self-righting bar extends up and outward from the robot, acting as a lever arm to push against the ground and shove it back up right. The shell was manufactured with a 50 degree slant to counteract horizontals and encourage more of a glancing hit than a direct one. The shell is also be manufactured out of a harder steel than Chonkii, which was made from un-hardened A36. The new shells are made from heat-treated 4140 steel, to prevent large dents that will cause the shell to wobble when it spins. More traction is needed to successfully compete with the speeds of the other robots, so the previous method of hot glue will be experimentally tested against new specially applied spikes.
High Level Design Overview
At its core, Chonki is designed to absorb large hits and win through attrition. Historically, RoboJackets drivers have not been particularly skilled. Chonkiii’s full body shell ensures that, when spun up, Chonkiii does not have a clear weak spot. The tapered shell is ¼” thick and weighs 24lbs. To accommodate for the increased weight, Chonkiii uses a shuffling drive system and utilizes a 150% weight bonus.
Chassis System
Overview
The overall frame of the chassis forms a cylinder that fits inside of the rotating shell resting on top of it. The self-right bar extends from the top of the center shaft to enable the bot to re-right itself if it is ever flipped on its top. The HPDE side plates on each side of the bot provide protection for the internal electronics while also not adding much weight. These features can be seen in the image of the chassis below.
<PUT IN PICTURE>
Top Plate
The top plate is made from waterjet 1⁄4 th in Al 6061. The plate includes hole locations for the two weapon motors, the four weapon rollers, the motor mounts, and side plates to attach to. The triangles are positioned on the top plate for weight savings.
<Top Plate>
Bottom Plate
The bottom plate is made from waterjet 1/8th in Al 6061. The plate has locations for the inner side plates on either side. The center four holes are for mounting the center shaft mount.
<Bottom Plate>
Side Plates
The outer side plate is made from waterjet 3/16th in Al 6061. The plate has milled circles for the drive bearings. It attaches to the top plate and is secured horizontally by the standoff.
<Outer Side Plate>
The inner side plate is made from waterjet 1/4th in Al 6061. The plate has locations for the motor mounts, drive bearings, and weight savings.
<Inner Side Plate>
Drive System
Chonki utilizes a shuffler system for drive. It consists of two shuffler modules, each with 4 UHMWPE feet. The feet sit on two parallel, keyed cam shafts. These allowed for the four feet to be positioned 90 degrees from each other, so feet would always be in contact with the ground through the cam shaft's rotation. To fit inside the feet get smaller as they move away from the chassis. The longer feet have fillets to clear the rollers and support which they sit under. The cams have offset keyed holes to accommodate the shafts and sit inside circular cutouts in the feet, which keep them parallel with the ground as it walks. The use of the shuffling system allowed Chonki a weight bonus, bringing the max weight to 45 lbs.
Foot Profile
The shuffler feet are shaped as such for several reasons. The decreasing lengths are such that the module will fit inside the circular profile of the shell. In the future, the lengths could be further shortened so that the modules could have armor plating in front of them in case a weapon is able to penetrate the shell. The downward slopes of the feet are to provide space for the rollers on which the shell rides. The needle roller bearings are placed into the circular cutouts.
Cams and Bearings
The cam profile is updated from Apachi. This version allows for a single cam profile and greatly simplifies shuffler manufacturing. Using a shaft and key that we have a broach for would be better than waterjetting and removing taper with a jank key-turned-broach.
Drive Gears
The drive gears were offset at around a 45 degree angle. Replacement gears should be purchased as the tended to get worn down after prolonged use.
Weapon System
Design Considerations
Since the weapon on this bot also serves as its armor, it was imperative that the weapon be large enough for the robot to fit inside. An additional constraint was that it must be small enough that a reasonable thickness could be attained while still remaining under the desired percentage of the total weight of the robot (~50%).
Shell Design
Shell was milled out of a 250 lb block of A36 steel. It took forever but was very effective in absorbing damage.
Pros:
- Less expensive than the nested ring design
- Made from one solid piece so it didn't have connection points to fail at
- Lives up the it's name, super THICCC
- Its SHINY!
Cons:
- Expensive, had to get Speed Machine to have them use a larger machine to mill the shell out.
- One piece, parts that got damaged on shell were not replaceable - dents needed to be pressed or hammered out.
Weapon Shaft Interface
A tapered roller bearing fits into a housing that is attached to the top of the shell.
Weapon-Drive Mechanism
- Inspired by Hyperpolarized, it was later decided to drive the weapon by using a single driven wheel at the top of the bot, with rollers along the surface to give additional support. A central shaft was used as a dead axle support.